Pilots
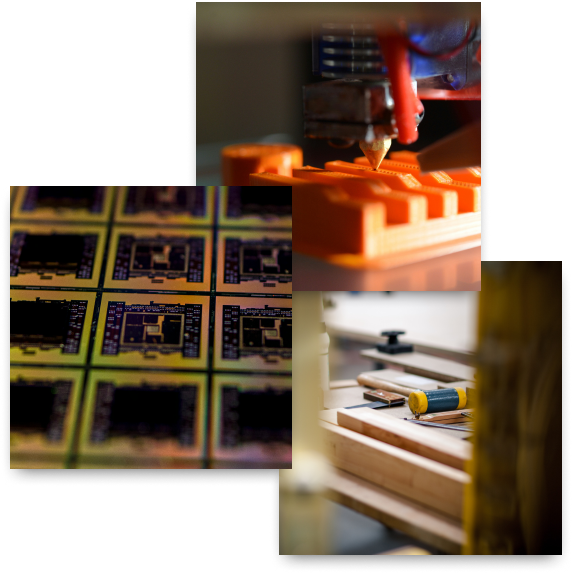
Pilot #1
Improving Automation & Supply-Chain Resilience in the Furniture Industry
Furniture manufacturing companies, especially those with limited digital technology support, face inefficiencies, delays, and a lack of visibility in their supply chains. Pilot #1 aims to address these issues by proposing Smart Manufacturing as a Service (MaaS) solutions, improving automation, optimising supply chain operations, resilience, and decision-making.
Stakeholders Snapshot
The industrial partner, Micuna, specialises in children’s and childcare furniture manufacturing and logistics. DHL will also be a partner, bringing expertise in logistics services. Technical support will be provided by AIDIMME Technology Institute.
Future Situation/Solution
The pilot aims to demonstrate how the Intelligent Manufacturing Custodian (IMC) can monitor production activities, detect anomalies, find replacements for supplies, and optimise logistics. The IMC will set up an automated workflow, detect anomalies, and provide decision-making support for managers.
Data Sources & Current Situation
Data sourced from ERP (Enterprise Resource Planning) systems, materials, processes, supplier performance, inventory levels, shipping times, and equipment performance.
Micuna faces challenges in demand planning, supplier management, and communication, leading to lost sales, excess inventory, and inefficiencies due to manual processes and forecasting difficulties.
Improvements, Performance Targets & KPIs
Expected improvements include better risk identification, reduction of quality incidents and on-time delivery issues, stock reduction, increased customer satisfaction, environmental performance improvements, and enhanced partner relationships. Targeted improvements range from 5% to 70% across various metrics.
Pilot #2
3D Printing Network as-a-service to Improve Resilience & Mitigate Unexpected Disruptions
Additive manufacturing technologies, while promising, face challenges such as occasional process failures, material limitations, and slow production times, in addition, due to their flexibility, the production value chain is constantly changing affecting every and each of the 3D printing steps and therefore the lead times. Pilot#2 proposes a cloud-based 3D printing network to provide decentralised and distributed production, enabling rapid response to unexpected events, absorbing peak demand or addressing very specific material requirements, and optimising production in various sectors.
Stakeholders Snapshot
The industrial partner, AIDIMME Technology Institute, specialises in metal-processing, wood, furniture, packaging, and construction technologies, providing support to associated companies. Technical support is also provided by AIDIMME Technology Institute and Nunsys.
Future Situation/Solution
The Intelligent Manufacturing Custodian (IMC) can control production across the network, rescheduling based on criteria like location, printing queues,material availability and even carbon footprint. Partnering with a coordinated 3D printing network allows for decentralised production, reducing reliance on global supply chains and mitigating risks.
Data Sources & Current Situation
The production of a significant number of different references and amounts is currently managed using basic programs, leading to inefficiencies and limitations in response to unexpected changes.
It is not just production that is irregular, but the entire value chain, from the cost calculation to the part shipping and delivery which implies that 3D printing faces challenges such as limited materials that can be processed with very specific technologies, slow production times, and high costs.
Improvements, Performance Targets & KPIs
The 3D printing network offers benefits such as localised production, faster turnaround times, reduced carbon footprint, and increased product lifespan. Expected improvements include enhanced Overall Equipment Effectiveness (OEE), reduced critical events, shorter lead times, and lower energy consumption. Targeted improvements range from 5% to 50% across various metrics.
Pilot #3
Achieving Supply-Chain Resilience in the Semiconductor Industry
budatec GmbH, an SME in the semiconductor industry, faces challenges with supply chain disruptions due to limited digital support and supplier dependencies. Pilot#3 aims to enhance digital capabilities to achieve supply-chain resilience, optimise inventory, and improve fill rates using Smart MaaS solutions.
Stakeholders Snapshot
budatec GmbH specialises in manufacturing machines for semiconductor and solar sectors. DHL provides historical data and warehouse buffering to support a coordinated supply chain. Technical support is provided by Fraunhofer IPK.
Future Situation/Solution
The IMC, AI Platform, and Digital Twins enable predictive analytics to anticipate disruptions, digital twin modelling for virtual supply chain optimisation, collaborative planning tools for improved communication, and circularity strategies to extend product lifespan and enhance reparability.
Data Sources & Current Situation
budatec GmbH faces shortages and unpredictable delivery times for machine parts due to supplier dependencies. Limited visibility and alternative sourcing options hinder proactive response to disruptions, increasing risk and capital tied up in stock forecasts.
Improvements, Performance Targets & KPIs
Expected improvements include decreased reshuffling post-disruption, reduced production time and stored capital, improved on-time delivery, and lifespan extension of machines. Targeted improvements range from 10% to 60% across various metrics.